News and Insights
Filter by
37 articles
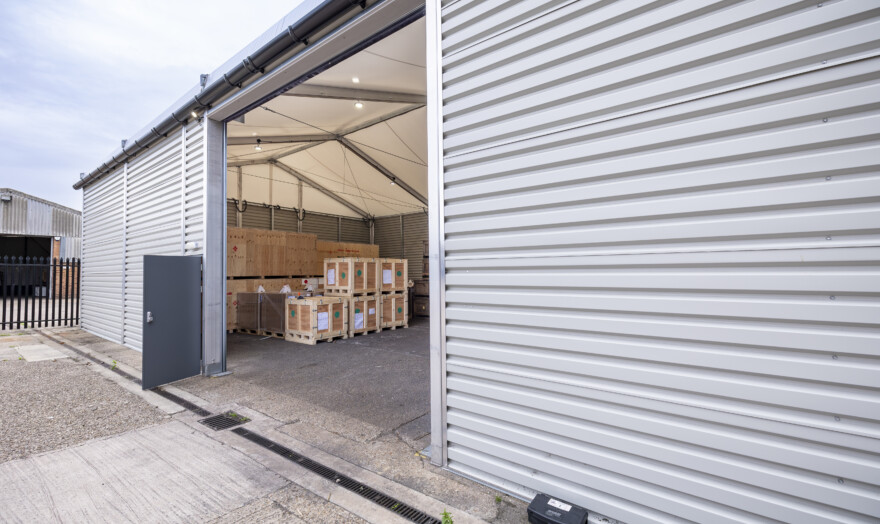
5 reasons a business might need a temporary structure
2 min read
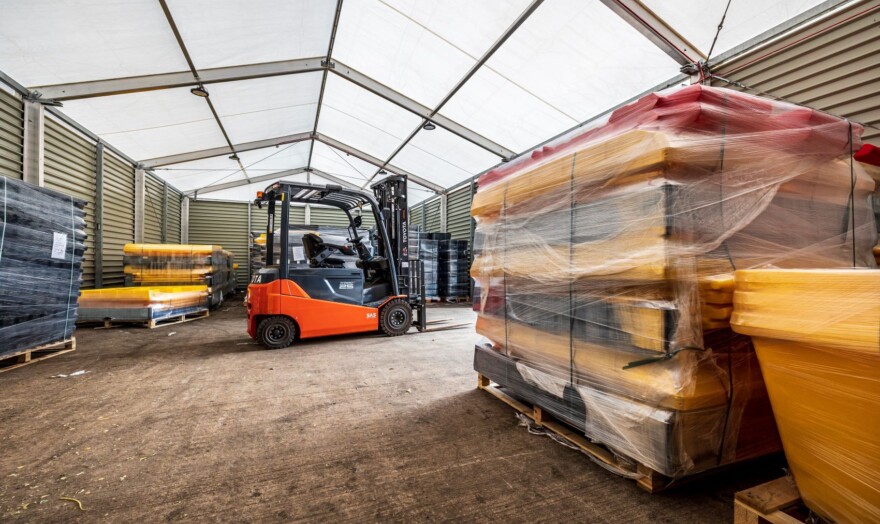
What is short-term warehousing and why is it important?
2 min read
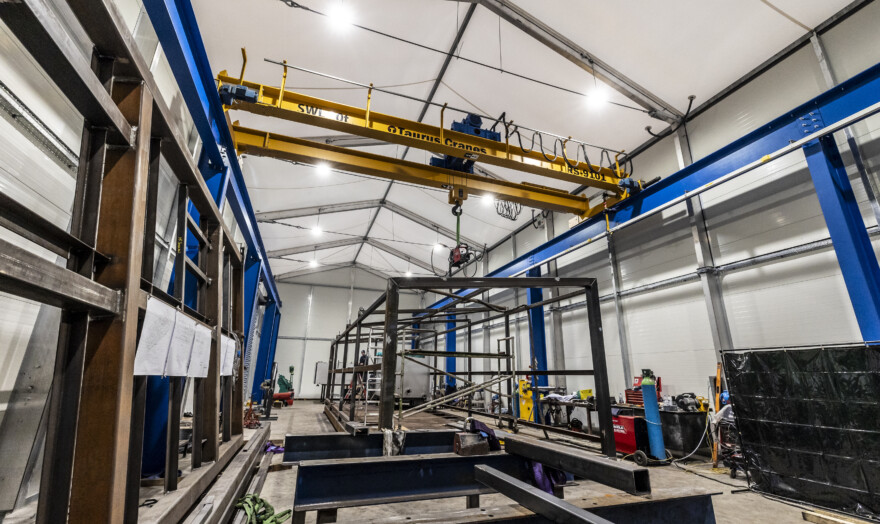
What are the cost saving benefits of temporary workshops?
2 min read
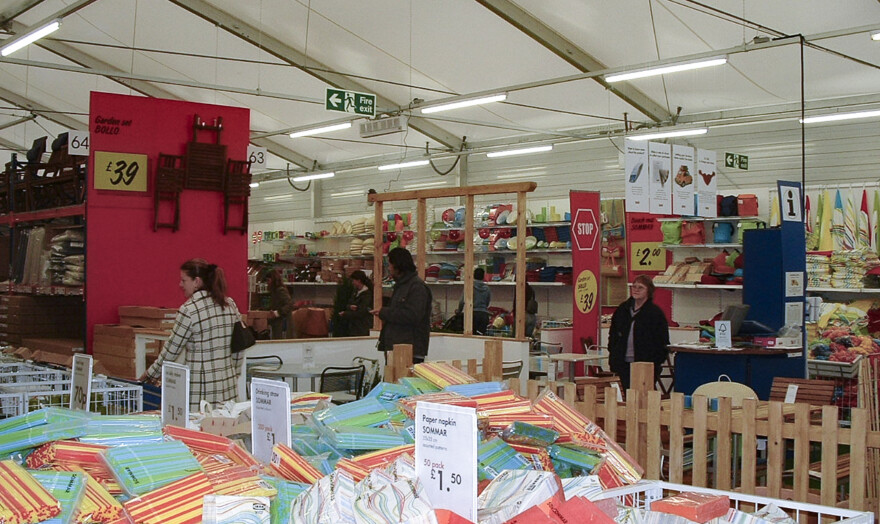
Why choose a temporary building for your seasonal retail space?
2 min read
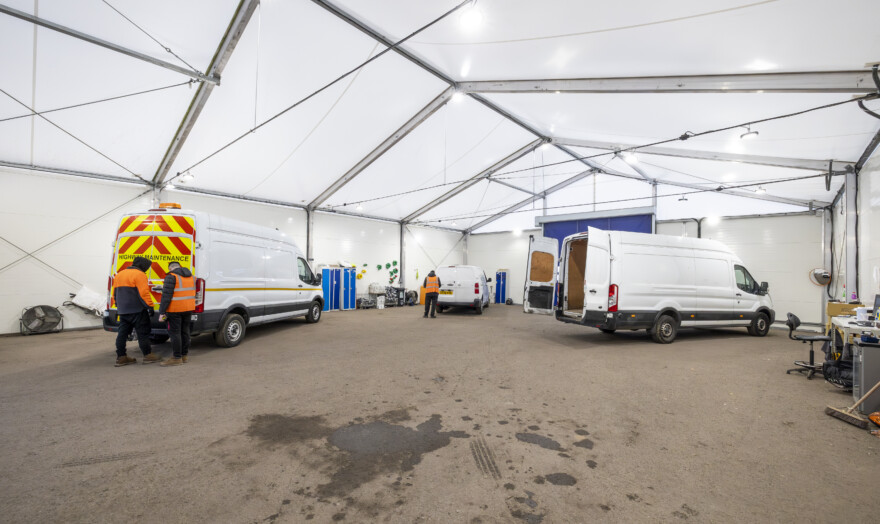
5 uses for temporary workshops
2 min read
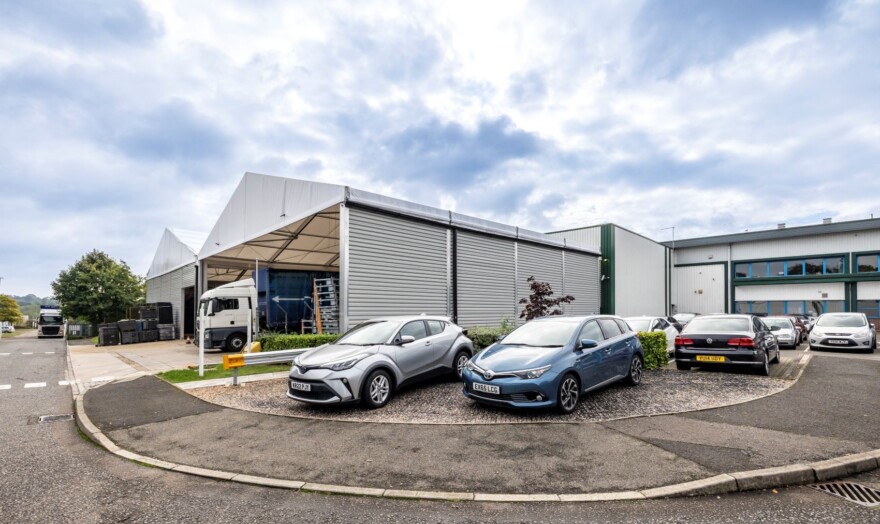
How warehouse loading bays can improve business efficiency
2 min read
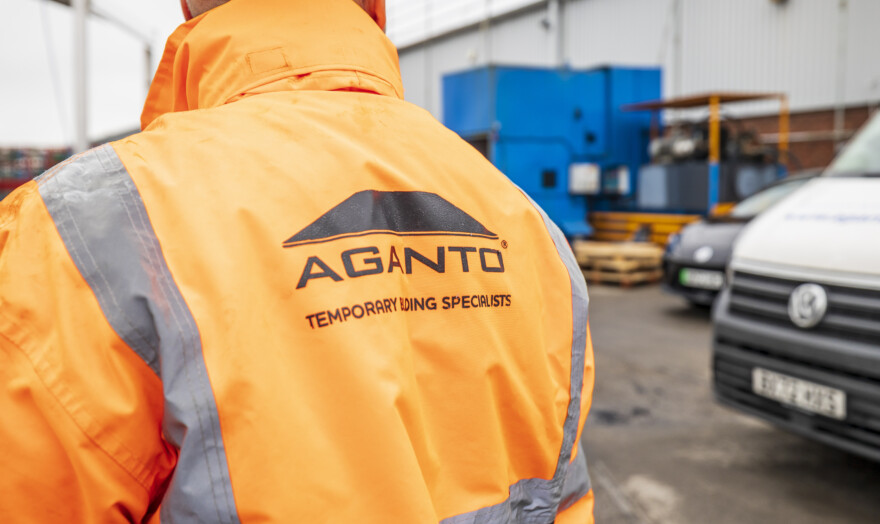
Aganto secures ISO accreditations
2 min read
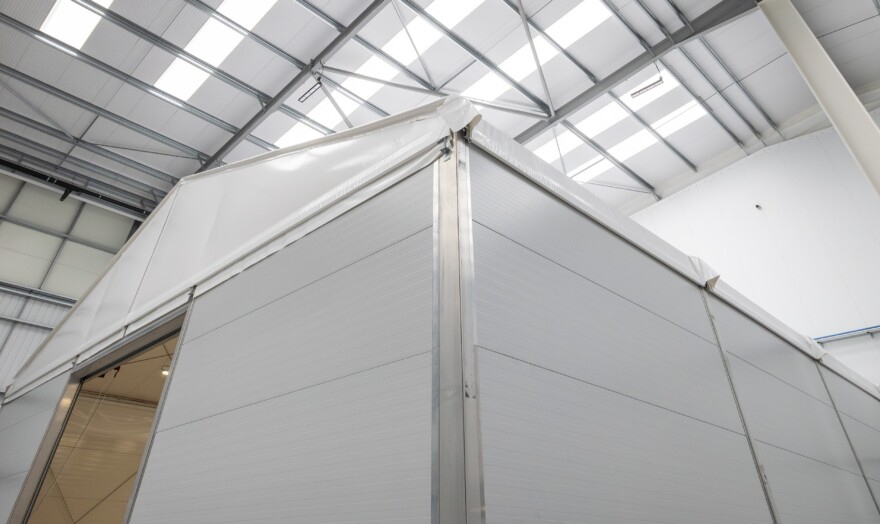
Can I install a temporary building inside my existing warehouse?
2 min read
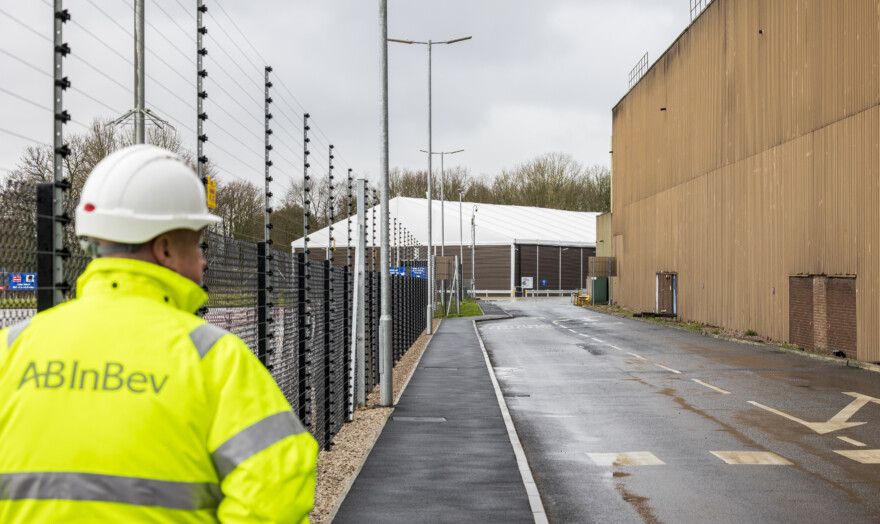
5 steps to a smooth temporary building planning application
2 min read
Everything you need to know about temporary buildings from planning permission, UK regulations and frequently asked questions.