Our projects
Our
Projects
Filter by
15 projects
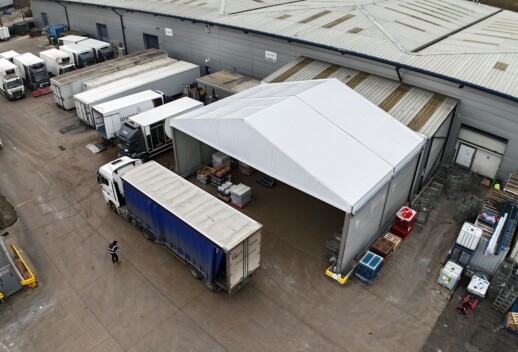
Savona Foodservice
/ Canopies
Enhancing logistics and distribution in the food services industry: A smart storage solution for Savona
View project
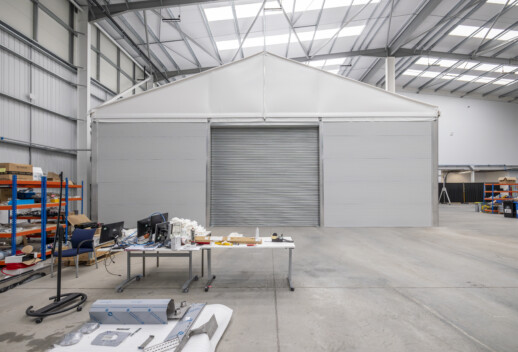
Temperature-controlled workshop space
/ Workshop
Creating a unique temperature-controlled environment within our client's existing warehouse.
View project
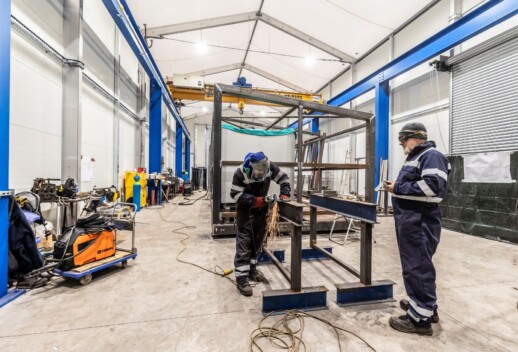
McQuillan Boiler Services
/ Workshop
McQuillan Boiler Services expand manufacturing capabilities with temporary structures
View project
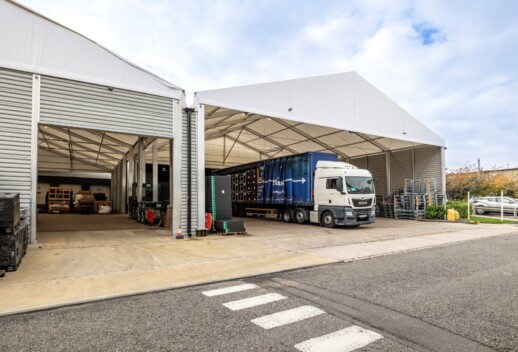
AGC Glass
/ Canopies
Installing bespoke canopy solutions to optimise our clients storage and distribution process.
View project
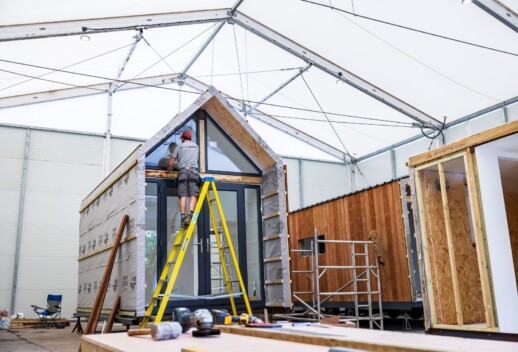
Glamping Fires
/ Workshop
Glamping Fires expand their manufacturing process with Aganto temporary workshop
View project
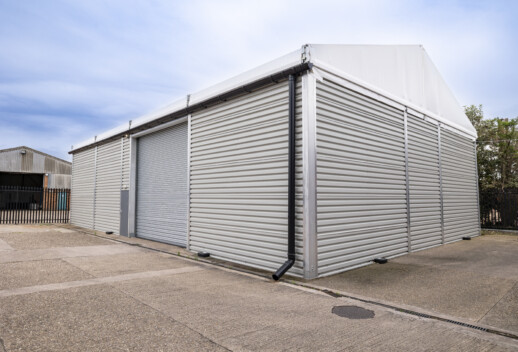
Howard Shipping Services Ltd
/ Temporary Buildings
/ Warehouse
Howard Shipping Services Ltd expand their storage space with an Aganto temporary warehouse
View project
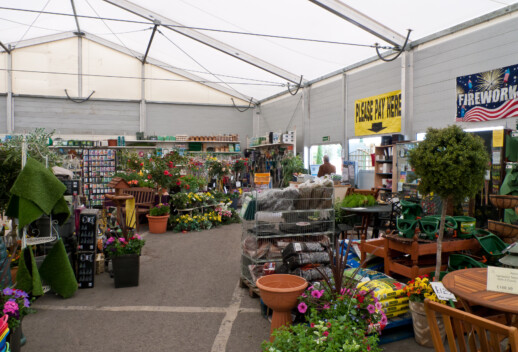
Waterways Garden Centre
/ Retail
When Waterways Garden Centre was damaged by heavy snowfall, they required an immediate solution to continue trading.
View project
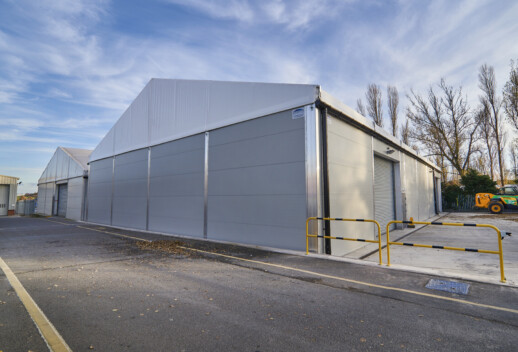
Bott Group
/ Warehouse
Bott Group wanted to increase warehouse storage and workshop space at their Ashby de la Zouch site to reduce off-site storage costs.
View project
Experienced,
hands-on,
industry experts
What makes us different
Our in-house industry experts are hands-on, from initial scoping to ongoing maintenance, delivering and installing temporary structures on time and within budget.
The cost-effective way to grow your business is with fast, flexible, high-quality temporary space